
Subscribe & Follow
Jobs
- Senior Organisational Development Specialist Cape Town
- Ombudsman Western Cape
- HR Generalist Vereeniging
- MBA Graduate Opportunity Cape Town
Hazardous environments call for zero tolerance on alcohol use
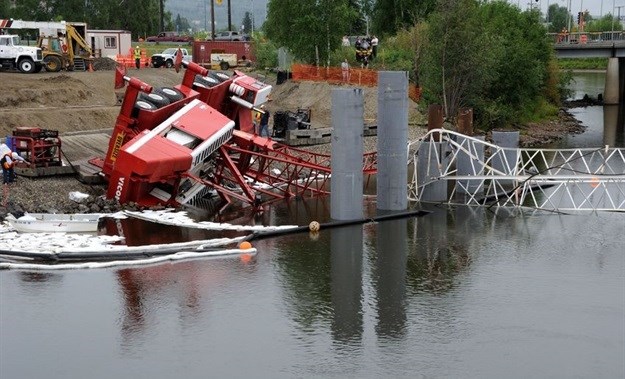
In order to mitigate this risk, warehouses need to adopt a zero tolerance approach to alcohol consumption in the workplace, backed up by effective policies as well as compulsory daily alcohol testing of every employee every day.
According to the Occupational Health and Safety (OHS) Act, employees are not permitted to be in the workplace under the influence of alcohol, no matter what industry they work in. Intoxicated employees may experience compromised cognitive ability and impaired decision-making, as alcohol is proven to increase risk-taking behaviour while decreasing inhibitions.
In the warehousing industry, the effects of alcohol consumption in the workplace can be catastrophic. Accidents with heavy machinery can cause serious injury and even death and, if it can be proven that the operator of the machinery was operating under the influence and management did not take steps to prevent this, then the company can be held liable for damages. Ensuring the safety and wellbeing of all employees within the warehouse workplace should be a top priority.
Policies needed
The first step is to adopt a zero tolerance approach, as mandated by the OHS Act. This requires that policies be put into place, which needs to include mandatory daily breathalyser testing of every employee, as they enter the workplace.
If only random testing is implemented, or employees are not tested every day, then alcohol usage is difficult to control because of the large number of staff involved in many warehouse ventures. In addition, education needs to form a critical component of any alcohol program, for even if people are tested on arrival, they may drink during the day. Education into the dangers of alcohol consumption in the workplace, with examples of the consequences of actions taken under the influence, can act as a significant deterrent.
Breathalyser linked to key access
New breathalyser technology too can play a role in ensuring compliance with zero tolerance policies. Key management solutions are in place in many warehouses in order to control and monitor who has access to keys for any physical asset, including heavy machinery such as forklifts and cranes. Intelligent, electronic key management systems provide a full audited history of key transactions, and new solutions incorporate a breathalyser function into this solution.
Regular key management typically requires the user to input a personal PIN number as well as his fingerprint in order to retrieve keys. The system then logs the time the keys were retrieved and by whom. The PIN and fingerprint must then be re-entered in order to return the keys, again logging the time and access code. With new breathalyser enabled solutions, users must not only enter a PIN and fingerprint, but also blow into an integrated breathalyser and demonstrate their sobriety by ensuring their breath alcohol is under the prescribed limit. Only then will the keys be released.
If the user does not pass the breathalyser portion, the keys will not be released, and the name of the person will be logged along with the breath alcohol reading. He or she will also then not be permitted to continue with work. To prevent alcohol consumption during the day while on shift, the same exercise must be repeated when the keys are returned. The system will create an alert and log the breath alcohol content of the operator should he or she fail the breathalyser upon return of the keys.
By ensuring effective policies are in place and by utilising advanced technology such as breathalyser-enabled key management systems, warehouse management can minimise the risk associated with alcohol consumption in the workplace. In addition to reducing risk, warehouses can also benefit from sober employees who require less time off, and who are less likely to cause accidents and breakages to assets and stock, not to mention avoiding workplace injury and fatality.
While new breathalyser systems will always require an upfront investment, this is typically minimal and will pay itself off quickly, effectively delivering long-term cost savings as well as OHS compliance.
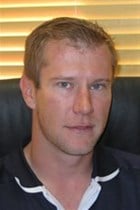
About Rhys Evans
Rhys Evans is the Director of ALCO-Safe, suppliers of superior drug and alcohol testing equipment and accessories throughout AfricaRelated
Public comments sought on draft Construction Regulations 6 hours 7 medical emergencies every workplace should be prepared for 7 Mar 2025 Temporary help required: Employers guide to navigating COIDA 6 Mar 2025 OHS isn't just physical: Why employee mental health is also your business 18 Dec 2024 Prioritising construction site safety, a vital commitment 25 Jun 2024 Branching into South Africa? 5 legal facets you shouldn't overlook 24 Jun 2024 George building collapse: 44 remain missing 10 May 2024 When zero-tolerance policies backfire: Dismissal for cannabis use at home ruled 'unfair' 7 May 2024
