
Subscribe & Follow
#AfricaMonth
Jobs
- External Sales Representative - Exports Vereeniging
In the news
AEL predicts increased use of electronics in mining industry
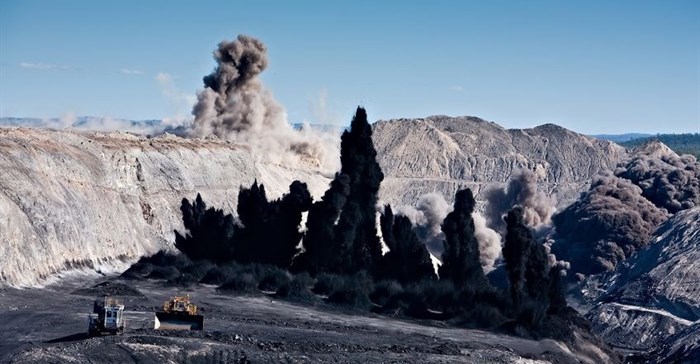
This is why electronic detonators are leading the charge towards reaching optimal blasts, right down to the correct millisecond. "Blasting companies need to collaborate further with their customers to look for efficiencies and approach situations more innovatively to drive cost reductions," says Carlos Paz, technical manager at AEL Indonesia.
He says that electronic detonators are helping to optimise processes all along the mining chain as products such as DigiShot Plus electronic system allow for new flexible blast designs, possible with electronic delays between one millisecond, all the way up to 20 seconds.
However, there is no one-size-fits-all timing when blasting. All related factors, including the type of rock, need to be taken into consideration.
Optimal delay timing
"While electronics have been on the market for some time, a small proportion of operations know how to identify the optimal delay timing. One of the most effective ways of determining this is by carrying out ground response and face velocity analysis in order to obtain data on how the rock mass responds to different parameters of drill and blast design," Paz explains.
Optimum timing leads to greater vibration control and fragmentation of the rock, which provides a reduction in the cost of operations. Such costs include a reduction in fuel for vehicles needed to move the fragmented rock as well as improved efficiency of crushers and mills due to reduced rock size.
Paz highlights AEL's Gunung Bayan Pratama Coal (GBPC) ground response case study in Indonesia which examined how the ground reacted to the detonation of explosives in terms of time through the use of high-speed cameras, laser profiling and use of dedicated AEL blast design software.
Higher burden relief
"By collecting and analysing the data, AEL recommended higher burden relief in order to allow enough time for the rock mass to heave and generate free face for the following rows and avoid back break. Quick intra-row delay was also suggested to avoid the loss of gasses between the stratums which also were observed in the filming," Paz says.
In addition to these suggestions, AEL managed to identify the optimal delay time and applied DigiShot Plus electronic system to achieve an increase on the mine's productivity to 10% over the target, which Paz says highlights the benefits of electronic systems.
Given these results, Paz and his team predicts that in the next few years the increased use of electronics and the predictability of performance and outcomes will see greater market share growth in South Africa, Indonesia and the rest of AEL's markets.
